Call us: +44 (0) 1202 868000
Don’t leave the safety of your workforce to chance
Join the hundreds of companies that use a ZoneSafe proximity warning alert system to keep their worksites safe and protect their workforce every single day.
Reduce the risk of
worksite accidents
ZoneSafe proximity warning alert systems
reduce the risk of accidents between
pedestrian workers, vehicles and assets.
Watch the animation to understand how
ZoneSafe creates a safer workplace for
worksites worldwide.
Why does your worksite need a proximity warning alert system?
- Do your staff work near moving vehicles and machinery?
- Do your drivers have blind spots or carry obstructing loads when operating vehicles?
- Does your worksite suffer with restricted visibilty or dimly lit areas?
- Are your workers ever complacement about site safety?
If you answered “yes” to just one of these questions, you’ve identified at least one area where your staff could be at risk of injury. Yet keeping people and vehicles segregated on a busy working site is no easy task. Blind corners, vehicle blindspots, concealed entrances, obstructions, poor visibility, and unexpected behaviours all increase the risk of collisions.
Zonesafe proximity warning and alert systems create a detection zone around people and vehicles so that dangers are detected, workers and operators are alerted (often before they can be seen), and collisions are avoided.
Because… everybody deserves to feel safe, no matter where they work.
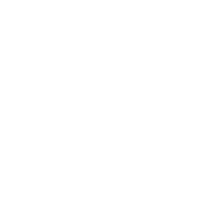
Help your employees
to feel safe at work
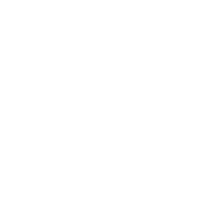
Protect your
employer reputation
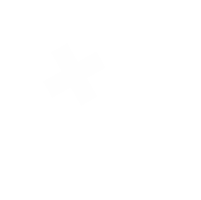
Improve your
safety culture
The Benefits of Using ZoneSafe Proximity Warning Alert Systems
- Dual detection of approaching workers and vehicles for greater awareness of potential risks.
- Maximize safety by alerting drivers and workers of dangers around obstructions, in blind spots or poor visibility.
- Comply with safety legislation and avoid large fines.
- Prevent completely avoidable accidents when pedestrians are required to work in close proximity to workplace vehicles.
Some of the clients we have worked with:

All of your proximity warning alert systems, in one place
Our versatile range of solutions are designed to suit your worksite, your operations and your procedures.
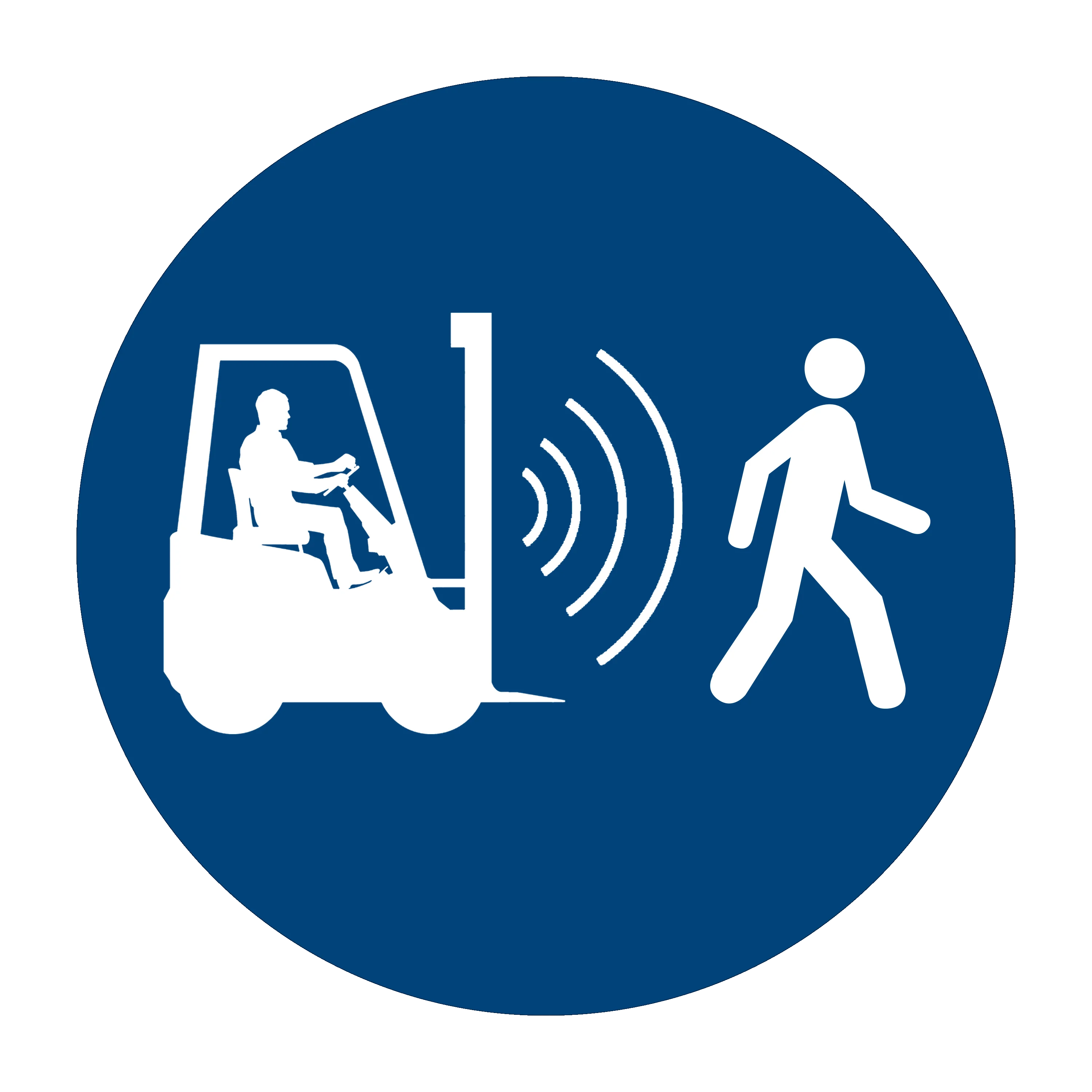
Pedestrian Detection & Alert
Create a detection zone around workers and vehicles so that the risk of a worker being struck by a moving vehicle is detected, and collisions avoided.

Vehicle to Vehicle Warning
Provide an early warning to vehicle operators in proximity to each other so that the risk of a collision between vehicles is detected, and collisions avoided.
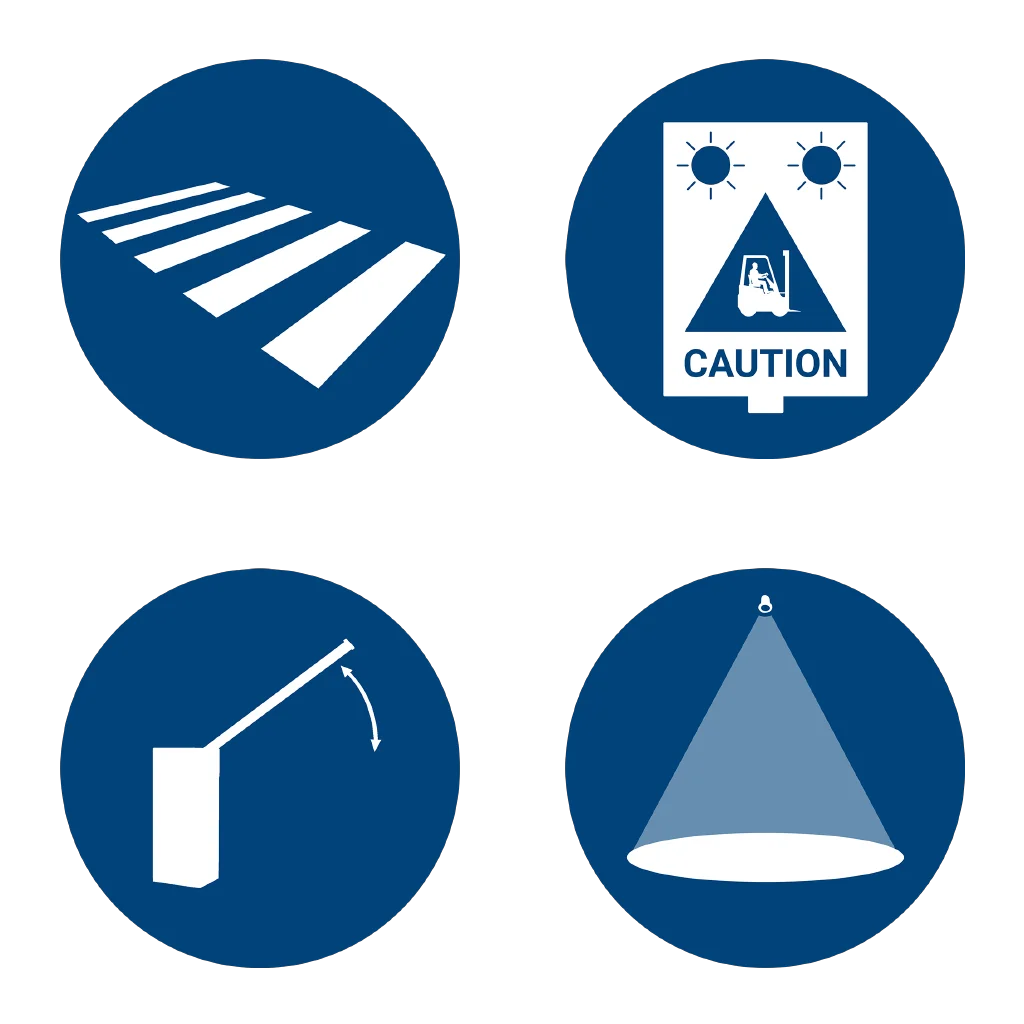
Active Signage & Area Warning Control
Provide worker and vehicle segregation, control, and visual warnings at pedestrian crossings, blind spots, and intersections so dangers are detected, and collisions avoided.
Risk reduction doesn’t need to be difficult
We make it easy to find a solution that works exactly as you want it to.
Book a free safety
consultation
It all starts with a conversation
so we can understand your site
needs and recommend the best
solution for you.
Benefit from an
on-site demo
Test our equipment at your own
worksite to see for yourself how
easy it is to reduce collision risk
and feel safer in the workplace.
Detect risks and
protect people
You and your staff will feel
confident that they can protect
themselves and each other
around moving vehicles.
Latest ZoneSafe News
ZoneSafe proximity warning and AI camera detection – Finding the best solution to your site safety challenges
When it comes to safety, there is no one-size-fits-all solution. Every site will have its own unique challenges, so it’s important to first fully understand…
Read moreAll ZoneSafe proximity warning alert systems are manufactured and distributed by Avonwood Developments Ltd
See how ZoneSafe can provide a solution for you Get in touch